The end for ground faults
Press release - 17.09.2021
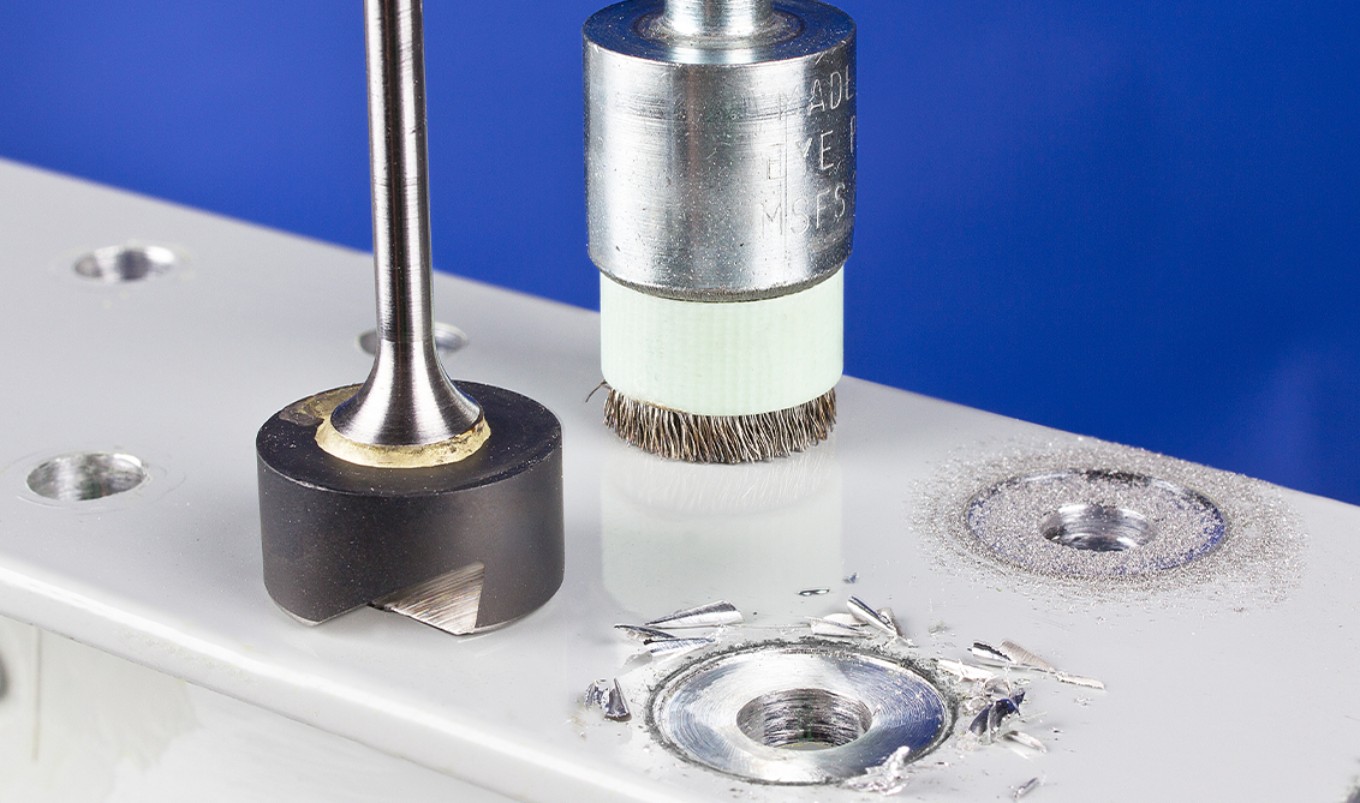
Ground faults are among the highest failure risks in aerospace and their consequences can be dramatic. Proper installation and care of ground points massively reduces these risks.
Fail-safe operation of electronic equipment and components in aircrafts is elementary to aviation. Flight control and management systems such as the autopilot, the flight management system, communication and navigation systems, as well as displays, sensors, mission and bus systems must function without failure.
In addition to the overall failure of systems or individual components, a ground fault is one of the greatest hazards to electronic operations. Ground faults can lead to erroneous measurements or even complete failure of the component in question. Therefore, the installation and maintenance of ground points, i.e., the points where equipment and devices are connected to the aircraft’s zero potential, is of particular importance. Also, the fact that important systems have multiple ground points shows the danger posed by ground faults.
Ground points are the locations on a conductive body to which the zero potential is assigned, which is the reference potential for all signal and operating voltages. From a technical point of view, a ground point must therefore have the highest possible conductivity. It should be flat in shape and have an even surface to ensure the greatest possible contact for connection to the system in question.
Ground points in aircraft are usually produced with brushes, since in most cases a coating or paint is to be removed from the desired point, the surface smoothed and the conductivity increased. However, machining with brushes is increasingly being replaced by the much more efficient and technically effective process of countersinking. For this purpose, a flat counterbore of nominal diameter is placed on the existing bore and, guided through the bore, a circular countersink of a few tenths of a millimeter is produced. This process is very fast and also has the advantage that chips are produced during machining and not dust. Handy battery-powered drives with offsets of 45 or 90° are used as drives. Suction systems can also be combined with them.
Well-known aircraft manufacturers have already changed their machining regulations for ground points to the effect that ground points may only be machined with so-called ground countersinks; also against the background of the updated REACH regulation, which states that toxic dusts, which are produced during the machining of aluminum, primer and paint and can be inhaled, must be minimized and extracted.
In addition, ground countersinks not only deliver the better result from a technical point of view, but also lead to a halving of tool costs and a significant reduction in machining time when viewed from an economic perspective.
For many years, the Marienheide-based manufacturer of tools for surface machining, PFERD Tools, has been a leader in the development and production of ground cores. PFERD developed this technology and has established a global key account management for the aerospace sector.
About PFERD Aerospace:
The globally networked Key Account Management PFERD Aerospace has been intensively involved with the requirements of aerospace technology for tools for surface machining and cutting for more than 20 years. PFERD solutions are successfully used in the areas of Engine, Component, Line, Airframe and Modification. The key account team is active and available with a focus on problem solving, cost effectiveness, process optimization and ergonomics.
About PFERD:
August Rüggeberg GmbH & Co. KG – PFERD Tools (www.pferd.com) is one of the leading manufacturers of tools for surface finishing and cutting metals. The family-owned company from Marienheide with more than 200 years of tradition manufactures its products in eight production facilities and today offers a system program that includes more than 9,000 tools. 1,950 employees in 26 subsidiaries worldwide ensure a market proximity that is ideal for optimal consulting and supply.